Experience
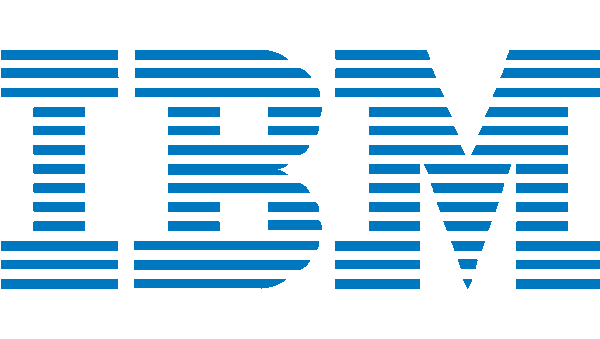
Executive Consultant
Simpler Consulting, an IBM Company2012 - present
Client Engagement Leader responsible for identifying and implementing state-of-the-art solutions for clients through the application of Lean Agile Thinking, AI, and the IBM Cognitive Cloud. Recognized subject matter expert on the integration of Lean Product Development within the broader context of a company-wide Lean Agile Transformation.
At the largest privately held life insurance company in the US, worked with executive leadership to integrate Lean, Agile, and the Scaled Agile Framework (SAFe) into a single cohesive approach for improving the work practices of more than 2500 software developers and IT operations personnel.
At a leading designer of industrial heaters, sensors, and controllers, implemented Agile / Scrum and classical Lean Product Development practices to enable five cross-functional product development teams to successfully bring a new modular I/O controller to market.
At a multi-site hospital network in the San Diego area, coached a cross-functional team of health care professionals and software developers in the use of Agile / Scrum techniques to successfully deploy an IT solution which standardized physician order entry across the network to achieve better patient outcomes at lower costs.
At an industry-leading designer of commercial food service equipment, coached multiple product development teams in the application of Lean Agile methods for both hardware and software applications, enabling them to integrate Internet-of-Things (IoT) technologies into their product line to improve work flow in the kitchen.
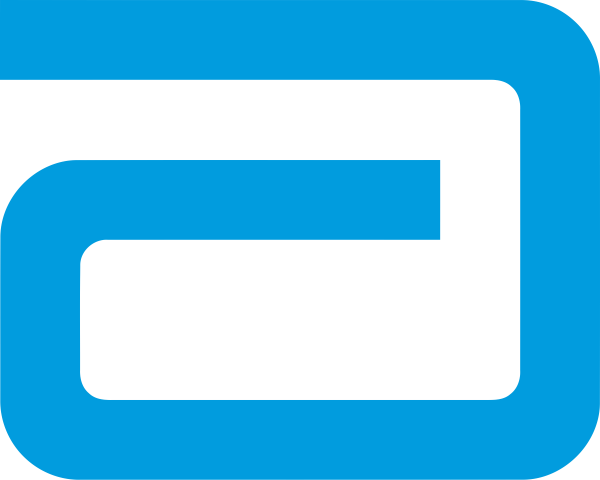
Director, Design for Excellence
Abbott Cardiovascular2010 - 2012
Accountable for implementation of the division’s Design for Excellence (DFX) initiative – a fusion of Lean Product Development, Agile, and Design for Six Sigma (DFSS) disciplines. Responsible for directing the activities of Agile Project Managers, Six Sigma Master Black Belts, and Six Sigma Black Belts to proactively identify and remediate design issues on stents, guidewires, and catheters.
Product owner for a $1.2M project to develop an automated vision system for the inspection of metallic stents and bioresorbable vascular scaffolds.
Responsible for identifying, planning, and executing process characterization studies during new product development to decrease unit cost and increase manufacturing yield.
Responsible for developing and implementing Agile Project Management practices in support of the division’s Lean Product Development strategy.
Led the formation a division-wide community of practice and the design and deployment of a comprehensive training program to institutionalize DFX principles and methods.
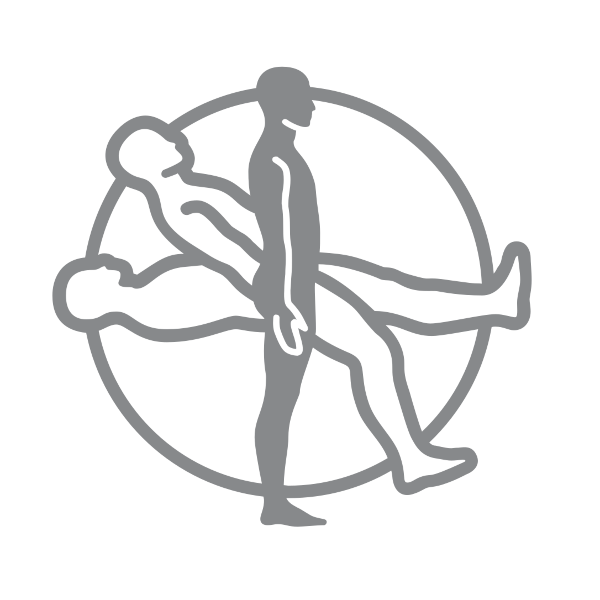
Director, Lean Six Sigma
Medtronic Spine and Biologics2006 - 2010
Accountable for oversight of all operations and quality projects within the Spinal & Biologics division. Responsible for implementing the Operational Excellence strategy for the division and driving cross-functional adoption of Lean, Six Sigma, and Project Management methods.
Directed the activities of Project Managers, Master Black Belts, and Black Belts to successfully complete over 60 projects saving more than $8 million.
Directed project work to reduce instrument scrap by more than $2 million over 12 months.
Provided operational oversight of a $500,000 project to deploy a computerized data acquisition system for incoming product inspections.
Led multiple “Tiger Teams” to address critical manufacturing issues with internal and external suppliers. Increased the manufacturing process capability (Ppk) for a critical spinal implant from 0.68 to 1.64, resulting in a $200,000 savings in material scrap reduction
Facilitated work to redesign the division’s New Product Development Process. Drove adoption of best practices in program and project management.
Deployed a scalable Project Management methodology to expand proven capabilities in Lean Six Sigma and drove adoption of fundamental PM principles throughout the division.
Lead trainer / recognized expert in Lean, Six Sigma, and Project Management. Delivered training to 200+ employees from multiple Medtronic divisions.
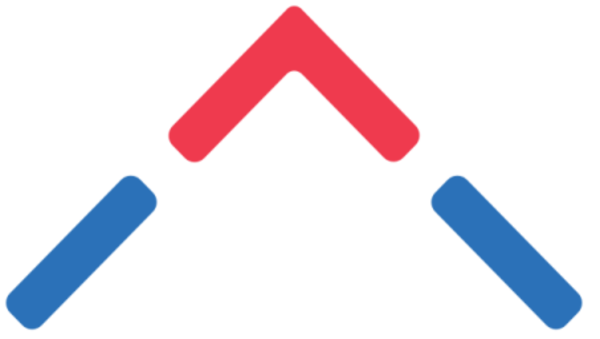
Six Sigma Master Black Belt
ServiceMaster2002 - 2006
Accountable for driving business cost reduction activities and management oversight of 17 Black Belts within a $3 billion home services company. Responsible for the Six Sigma interface with the corporate Project Management Office (PMO) and the processes for project selection, prioritization, resource assignment, and performance monitoring.
Led and mentored cross-functional continuous improvement projects worth more than $8 million in bottom-line savings by applying proven Six Sigma principles and techniques.
DFSS lead for design and testing of the “Smart Truck” program – a vehicle-based wireless technology platform deployed in more than 10,000 field service vehicles.
Led efforts to fuse Design for Six Sigma (DFSS) and Software Development Lifecycle (SDLC) methodologies into a single cohesive framework suitable for a broad range of projects.
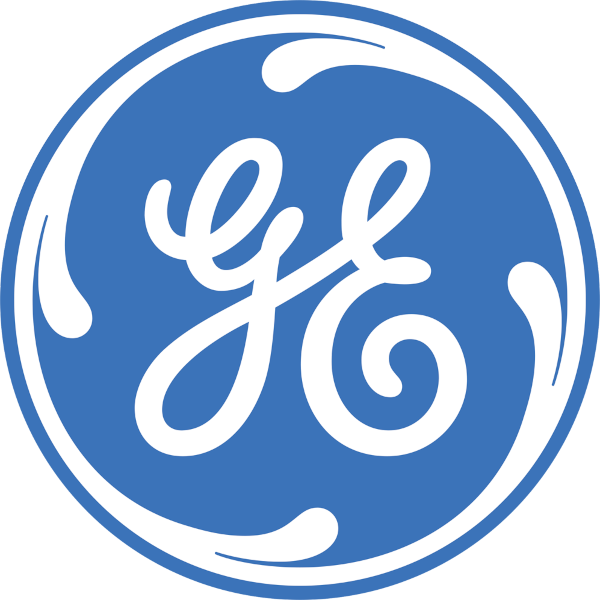
Six Sigma Black Belt
General Electric2000 - 2002
Six Sigma leader at the switchgear manufacturing facility within the Industrial Systems division of this $170 billion Fortune 100 company. Accountable for driving local cost reductions and implementing corporate global quality initiatives.
Reduced transportation costs by $100,000 annually using Six Sigma (DMAIC) analysis. Led efforts to negotiate reduced shipping rates with key freight carriers.
Delivered $1 million in bottom-line savings by streamlining the design engineering process for electrical switchgear products.
Responsible for improving GE product quality at Intel microchip fabrication facilities. Led field teams in root cause / corrective action assessments of in-service failures.
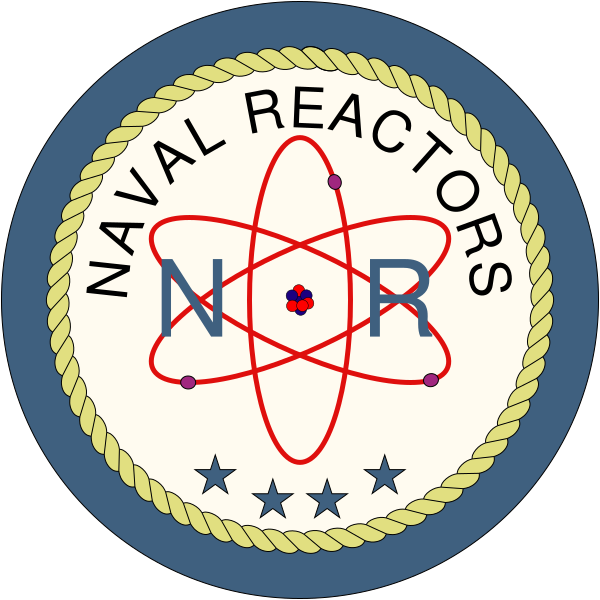
Project Engineer
Naval Sea Systems Command - Office of Naval Reactors - Code 081995 - 2000
Lieutenant assigned to the headquarters of the United States Navy Nuclear Propulsion Program. Accountable for the design, manufacture, installation, maintenance, and support of more than 185 valve designs installed in 70 nuclear-powered ships and submarines.
Responsible for oversight of manufacturing contracts worth $3.5 million annually.
Lead engineer for a $3 million dollar project to develop an improved hydraulic gate valve design for the next generation aircraft carrier, CVNX.
Responsible for a $2.5 million dollar study of metallographic, chemistry, and welding parameter variations encountered during valve manufacturing.
Reduced the cost of submarine valve repairs by over 400 hours through improved repair tools, test fixtures, and procedures.